The cleanest aluminium for the Cleanest Dirt Bike Ever
CAKE and Vattenfall have joined forces to build the Cleanest Dirt Bike Ever by 2025, decarbonising the supply chain of CAKE’s off-road electric motorcycle, the Kalk OR. Aluminium accounts for a quarter of the weight of the Kalk OR. But it represents 34% of the carbon emissions released in producing the bike. Aluminium is clearly a critical challenge to address in our decarbonisation journey.
The backbone of the automotive industry
It was no surprise to discover that aluminium parts add up to 25% of the weight of the Kalk OR. It’s by far the most widely used material in the bike, followed by steel at 9.5%, rubber at 8% and plastic at 4.5%. As aluminium is relatively light, it actually makes up a much bigger proportion of the bike’s total volume. Aluminium is a key raw material in all CAKE motorcycles and has served as the backbone of the automotive industry in many applications, because of its characteristics of being robust while being incredibly light and non-magnetic.
Aluminium in the CAKE Kalk OR.
However, as with all materials, there are also downsides with aluminium, predominantly the amount of emissions released throughout its value chain. Read more about how aluminium is made, here. For the Kalk OR, aluminium parts account for 27% of its production emissions with an additional 7% of emissions coming from the aluminium used in the battery, motor, brakes, controller and suspension, adding up to 34% of the bike’s total footprint. This means that to build the Cleanest Dirt Bike Ever, we need to find solutions for cleaner aluminium.
The impact of clean energy in reducing emissions
Primary (non-recycled) aluminium’s greenhouse gas emissions are mainly due to an energy-intensive production process. This makes the source of the electricity used in that process the most significant factor behind the size of its carbon footprint.
Emissions from primary aluminium production.
While the location of the raw materials can’t be changed, the emissions from aluminium production can be lowered dramatically by processing the metal in a location with access to clean energy, such as countries like Norway or Sweden, where more than 95% of the power produced comes from fossil-free sources.
To reduce emissions further, recycled aluminium is an option which requires only 5% of the original energy consumption to produce.
Finding the right partner for the Cleanest Dirt Bike Ever
In our search for the right partner to help decrease the aluminium footprint of Kalk OR, we searched the global market for clean solutions, looking for a partner with:
- The technology to develop clean products and plans to invest further in the field
- Access to clean energy throughout the value chain
- Transparency on its carbon footprint calculation and methodology
- A location close to home, to avoid shipping materials long distances
We selected a partner who shares not only our vision of a sustainable future but also transparency around carbon footprint calculations, one that has started its journey towards zero-emission aluminium production, just around the corner from our Swedish home: Hydro.
Hydro’s pathways to zero
The Norway-based aluminium company Hydro, is an established global player that’s already begun its journey to decarbonise its aluminium production process, and is on the road towards becoming a net-zero company. Hydro is committed to achieving net-zero emissions no later than 2050. But prior to that, the company is aiming to become an industry leader in delivering industrial scale zero-carbon aluminium by 2030. Achieving this goal is based on three pathways:
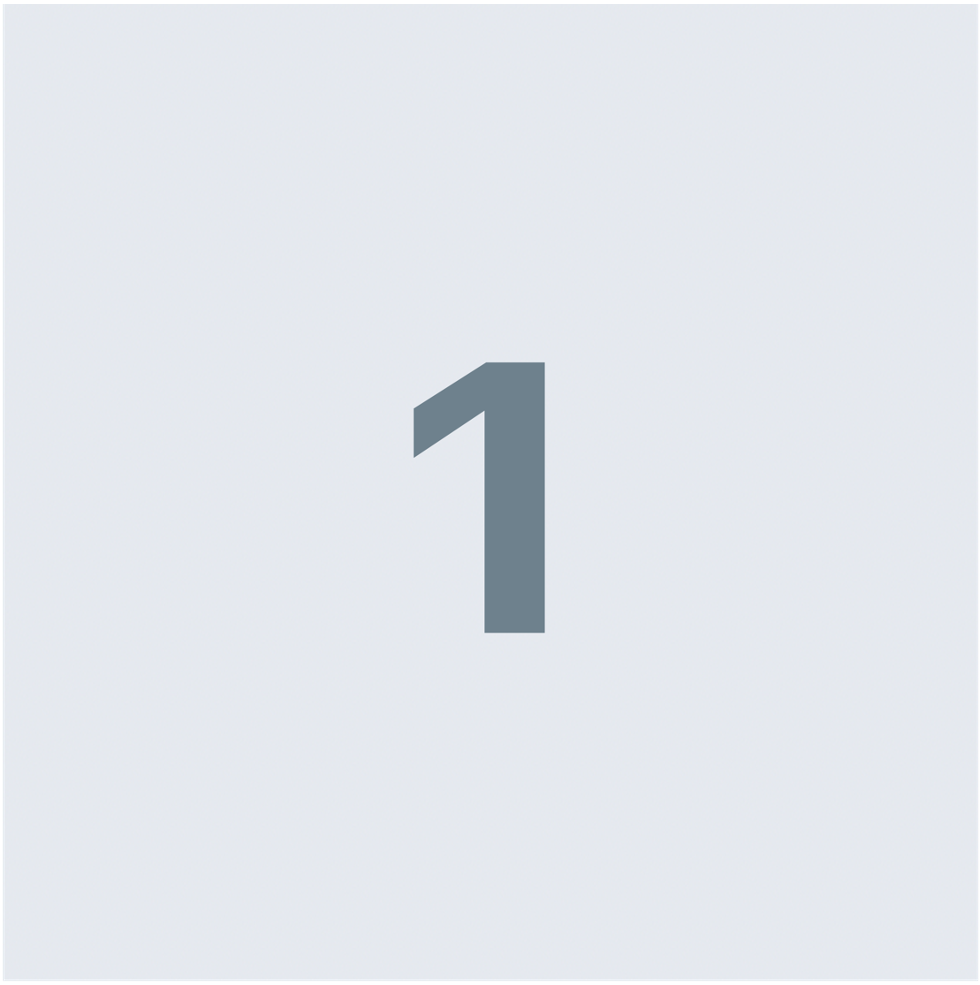
Recycled aluminium with decarbonised operations
Recycling of post-consumer scrap with decarbonised operations.
This will be made possible by Hydro’s aluminium sorting technology and alloying expertise, in combination with replacing natural gas with green hydrogen or electrical heating at recyclers and casthouses.
Timeline: The aim is to develop technology pilots by 2024, with the ambition to industrialise new technology by 2026.
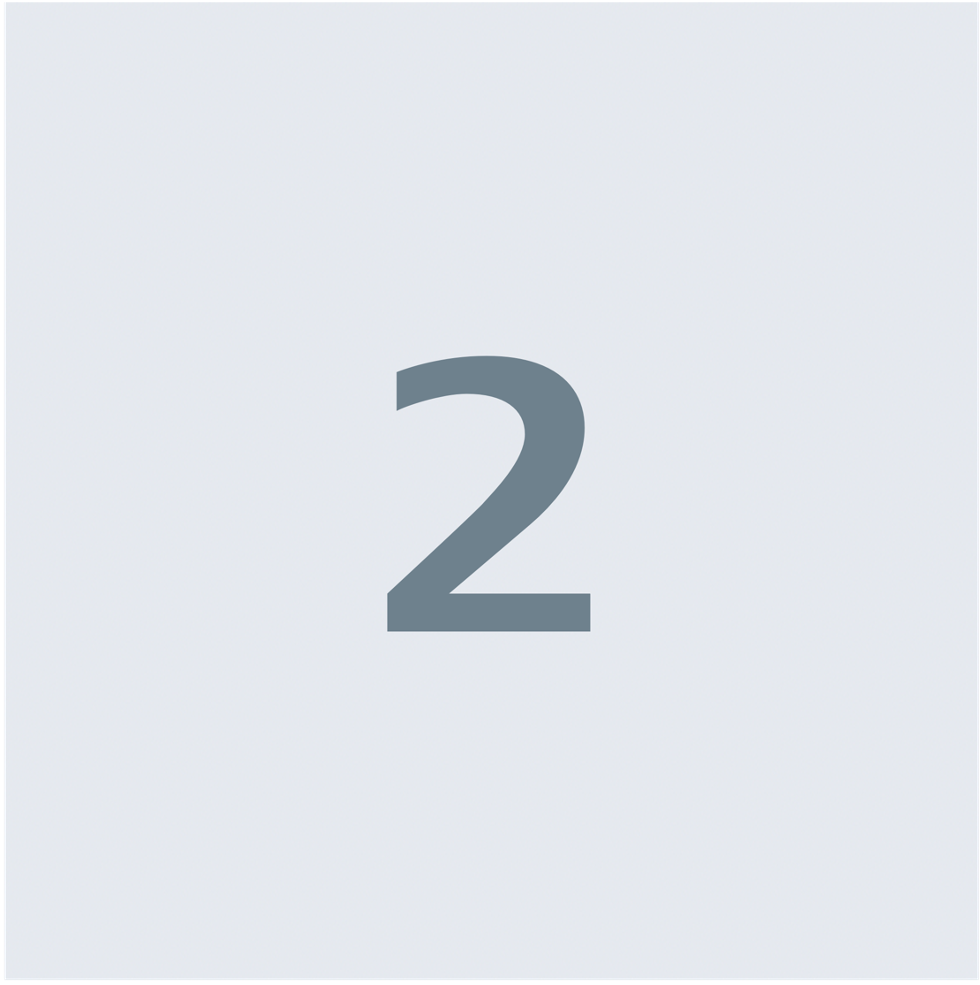
Primary aluminium with captured emissions
Carbon capture and storage (CCS) for existing primary aluminium smelters.
The most likely outcome will be a combination of off-gas capture and direct air capture to eliminate 100% of the emissions. This may include using bio-carbon in the anodes. Other improvements could be the use of inert anodes, although no solution currently exists, and a changed chloride process in which the alumina is converted to an aluminium chloride that can readily be processed by electrolysis. The chlorination needs carbon, but the carbon as well as the chlorine could be recycled in a closed loop.
Timeline: The goal is to have an industrial-scale pilot running by 2030.
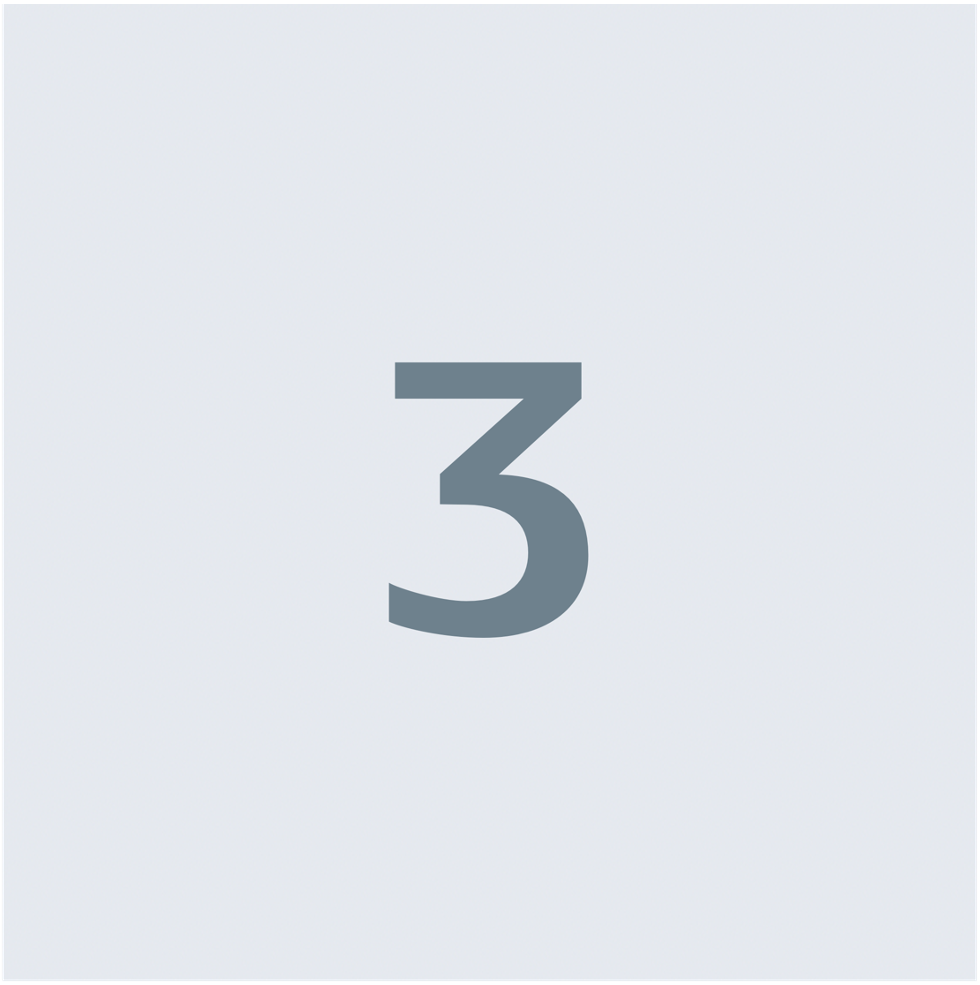
Primary aluminium with decarbonised operations
Development of Hydro’s proprietary HalZero technology for greenfield aluminium plants.
This is a technology where carbon and chloride are kept in closed loops, resulting in a fully decarbonised process, where the only emission is oxygen. It will fully decarbonise the smelting of aluminium, eliminating emissions from both electrolysis and anode baking, resulting in emission-free aluminium.
Timeline: If successful, the ambition is to produce first pilot volumes by 2025 and to have an industrial-scale pilot up and running by 2030.
The cleanest aluminium for the Cleanest Dirt Bike Ever
Today, the CAKE Kalk OR is made using primary aluminium processed in China. The carbon emissions from this metal are 16.6 kg CO2e per kg of aluminium. To succeed in our mission to reduce this to as close to zero as possible by 2025, the project will follow Hydro’s recycled pathway, providing decarbonised aluminium solutions within the project timeline with the potential to reduce the aluminium footprint in the Kalk OR from between 77% to 97%.
Options for the Kalk OR by 2025:
- Low-carbon primary aluminium Norway (4 kg CO2e/kg Al)
- 75% recycled post-consumer aluminium (2.3 kg CO2e/kg Al)
- 100% recycled post-consumer aluminium (0.5 CO2e/kg Al)
Emissions from 1 kg of aluminium.
The obvious solution would be to choose the 100% recycled content with close to zero emissions per kg, and implement it on all aluminium parts of the bike. But there’s a catch - as the near-zero carbon aluminium from Hydro is only available in small batches, which means it’s not yet available in all alloy options.
In 2022, Hydro produced the first 100 tonnes of aluminium from 100% post-consumer scrap, delivering a near zero carbon aluminium. But which recycled aluminium alloys will work on the Kalk OR?
The challenge of using recycled aluminium in a high-performance motorcycle
Aluminium isn’t just aluminium. Aluminium can be alloyed with other metals and non-metals, allowing it to take on different properties. There are more than 540 registered compositions available today.
The aluminium components in the CAKE Kalk OR are made from the 6061, 6082 and 7075 alloys. This is based on the mechanical requirements and manufacturing feasibility of the parts, designed to build a light high-performance motorcycle with clean aesthetics.
Using 75% recycled post-consumer aluminium processed in Sweden, Hydro can provide the 6082 and 6060 alloys. Hydro can also provide 6060 using 100% post-consumer scrap – the cleanest option available. 6060 is most frequently used in applications that require the highest quality finish and where strength is not the crucial factor. It’s often used in the automotive industry, however it’s not currently used in the Kalk OR.
This is where the really challenging work begins. Right now, we’re working to analyse and test which parts of the bike can use the different alloys available, depending on strength requirements and manufacturing processes, to work out exactly how the recycled metal can be implemented into the bike.
Aluminium alloy 6061 is the most commonly used alloy in the Kalk OR, because it boasts high strength when forged. It’s an alloy with structural strength, good corrosion resistance and machining characteristics. Unfortunately, Hydro does not supply the 6061 alloy with a large percentage of recycled metal.
So we’re investigating the possibility of using the 6082 alloy as a substitute. 6082 qualifies as a good choice for structural components, with existing applications including extruded trailer profiles for trucks. However, using 6082 as a substitute would require a rework of the mechanical requirements of the parts. This could mean an increase in weight or parts being out of dimension, leading to significant design changes.
An even bigger hurdle is the stiffer 7075 alloy which, like 6061, isn’t available with a high percentage of recycled metal. Replacing it with 6082 would potentially require more material to meet the same design requirements, due to a significant difference in the tensile strength between the two alloys. Again, the likely solution would be a rethink of the design of several parts.
Moving forward – re-designing our dirt bike to make it clean?
We’ve now identified the aluminium alloys which will be available before 2025. The next step is to work out how to fit them into the Kalk OR, potentially having to re-construct our entire bike to make recycled content work for the parts we need.
We also face challenges with manufacturing capabilities close to home. There are challenges with lack of forging options for the 6061 alloy in Scandinavia or nearby countries with access to clean energy. Moving to alternative manufacturing processes will have a major effect on several key components in the bike.
These challenges raise some fundamental questions: which recycled aluminium alloys best meet our needs, does it make sense to use cleaner materials if you require more of them and what level of redesign is appropriate in order to decarbonise our bike without compromising its performance?
All of these questions are interlinked. None of them can be answered in isolation. And solving one may well raise more.
But this is what we’re working on right now. Stay tuned to follow our progress.
We need you
We’re constantly looking out for partners to manufacture parts and supply materials in the cleanest possible way. We also want to connect with industry experts, researchers and other pioneers to join us and guide us on our mission.
Right now, we’re also looking for collaborators on the motor, the PCB and cabling among other parts. Feel free to reach out to us at cdbe@ridecake.com to join the ride.